What Is the Best Method for Concrete Leveling in Texas?
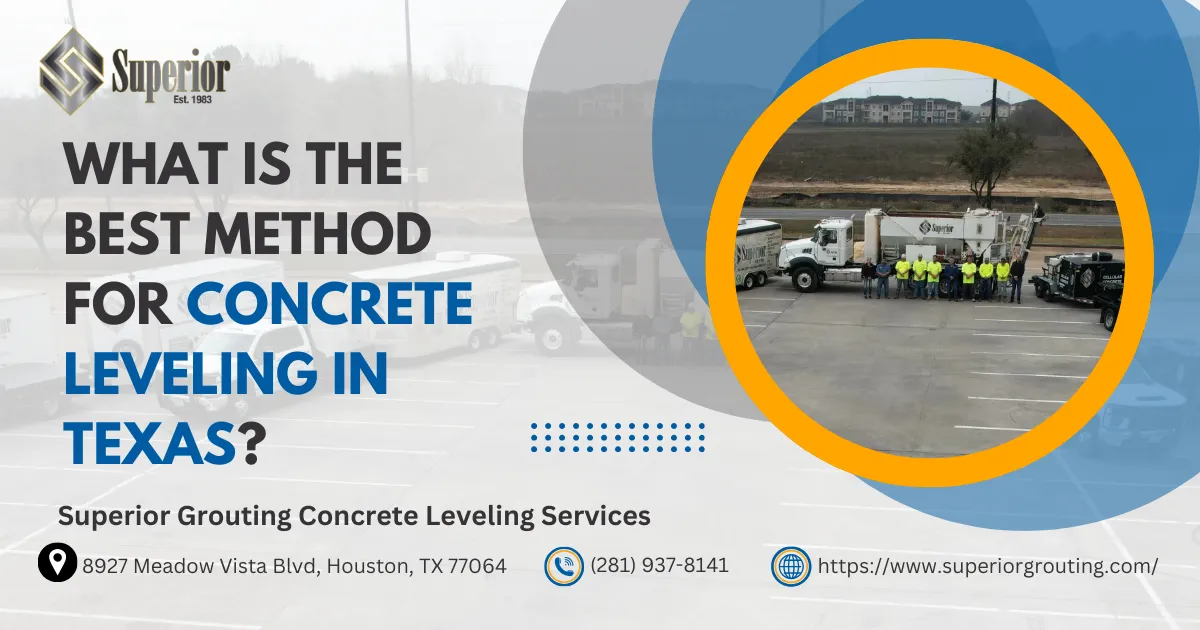
Expansive Gulf‑Coast clay, flash‑flood rainstorms, and year‑round temperature swings all conspire to make concrete become uneven on commercial, industrial, and municipal properties from Houston to El Paso. Trip hazards outside a distribution center, ponding water on a city sidewalk, or a sunken loading dock slab can interrupt operations, invite liability, and drive up maintenance costs. That’s why property managers inevitably ask the same question: “Which method of concrete leveling delivers the fastest return and the longest service life in Texas?”
For concrete leveling in Houston, polyurethane foam injection (also known as polyjacking or LEVELift) is generally considered the best method because it's faster, cleaner, more durable, and more cost‑effective than traditional methods like mudjacking.
Below, we’ll explore how different concrete leveling techniques stack up and why polyurethane foam injection has become the best approach for keeping critical concrete assets performing in the Lone Star State.
Key Takeaways
- Polyurethane injection outperforms mudjacking. Polyurethane foam injection—widely branded as LEVELift or polyjacking—has overtaken mudjacking at Texas industrial, commercial, and municipal sites because it lifts slabs in minutes, adds negligible weight, resists floodwater washout, and minimizes production downtime.
- Long‑term structural strength is superior. Closed‑cell foam bonds to the slab’s underside and stabilizes underlying soils, delivering compressive strengths above 100 psi and 15‑plus‑year service life—far longer than cement‑slurry lifts that frequently re‑settle within a decade.
- Minimal intrusion keeps facilities running. Small ⅝‑inch injection ports preserve finished surfaces, and 15‑minute cures let warehouses, hospitals, and transit hubs reopen traffic lanes the same shift—avoiding days‑long closures and detours tied to mudjacking or full replacements.
- Lightweight, hydrophobic foam protects clay soils. At roughly 2 lbs per cubic foot, the foam neither leaches fines nor overloads expansive Gulf‑Coast clays, making it the most reliable leveling strategy for flood‑prone pavements and slab‑on‑grade facilities.
- Professional crews deliver compliance and documentation. Certified contractors combine soil analysis, GPR utility mapping, laser monitoring, and post‑lift elevation reports—critical for ADA conformity, OSHA housekeeping, and long‑term asset management in Texas manufacturing and municipal infrastructure.
- Life‑cycle economics favor foam leveling. Although foam’s $6–$9 per‑square‑foot price slightly exceeds mudjacking, near‑zero downtime, longer service life, and elimination of demolition waste yield a lower total cost of ownership—often paying back within a single fiscal year.
Understanding an Uneven Concrete Surface in Texas
Daily thermal cycling and clay‑rich soils cause slabs to heave in summer and settle when the soil dries and shrinks. Heavy forklift traffic or constant 18‑wheeler loading can also compact sub‑grade soils, creating hidden voids beneath a concrete slab. Once the support disappears, the slab drops, cracks propagate, and surface water accelerates deterioration. Left unchecked, a simple trip hazard turns into a structural foundation repair problem—or worse, a shutdown for full slab replacement.
Texas building owners have traditionally relied on mudjacking (also called “slab jacking”) to fill those voids, but newer leveling methods have changed what’s possible.
Traditional Mudjacking: Filling Voids with Cement‑Slurry
Mudjacking involves injecting a thick, cement‑based slurry beneath a sunken slab through several small holes drilled in a grid pattern. As the slurry fills the void, hydraulic pressure lift[s] and level[s] the slab back to grade. Once the material cures, the holes are patched with mortar.
Strengths
- Uses inexpensive cementitious material that matches existing concrete density
- Familiar process for many contractors
Limitations
- Requires large‑diameter holes (often 1⅝ in.) that remain visible
- Adds roughly 100 lbs. of weight per cubic foot—risking future settlement
- Extended cure times (up to several days) delay reopening high‑traffic areas
- Slurry can erode under recurring Gulf‑Coast flooding, leading to repeat settling
In high‑volume industrial environments where downtime equals lost revenue, these limitations have pushed asset managers to search for a lighter, faster leveling solution.
Polyurethane Foam Injection: The Next‑Generation Concrete Lifting Technique
Unlike mudjacking, polyurethane foam injection uses a two‑part liquid resin pumped through ⅝‑in. ports. Once the components mingle beneath the slab, the resin expands into a dense, closed‑cell foam that gently raise[s] concrete back to its original elevation.
Key Advantages for Texas Facilities
- Speed – Foam achieves 95 % strength in about 15 minutes, so warehouses, hospital walkways, and municipal sidewalks reopen the same shift, avoiding costly rerouting.
- Lightweight – At roughly 2 lbs. per cubic foot, the material stabilizes without over‑burdening expansive soils.
- Water‑Resistant – Closed cells seal out moisture, crucial in flood‑prone regions from the Brazos to the Bayou.
- Clean – Minimal dust, smaller ports, and no slurry wash‑out keep sensitive environments—like food‑processing plants—code‑compliant.
- Longevity – Decades‑long lab data show foam retains compressive strength even after repeated wet‑dry cycles, giving owners peace of mind.
Because the foam fills voids, bonds to the underside of the slab, and resists soil washout, engineers consider it the best concrete leveling system for heavy‑duty pavement, airport aprons, and mass‑transit platforms.
Head‑to‑Head Comparison: Level Concrete Faster, Cleaner, and Cheaper
Criterion | Mudjacking | Polyurethane Foam |
Hole Size | ~1.5 in. | ~⅝ in. |
Added Weight | High (may settle again) | Negligible |
Cure Time | 1–3 days | 15 minutes |
Water Resistance | Moderate | Excellent |
Re‑do Frequency | 5–10 yrs | 10–20 yrs+ |
Typical Cost* | $4–$7 / sq ft | $5–$9 / sq ft |
*Pricing reflects 2025 averages for commercial projects in Texas. Foam’s longer lifespan and near‑zero downtime usually offset the slightly higher square‑foot cost, making it more cost‑effective overall.
Why Polyurethane Foam Is the Best Method for Commercial, Industrial, and Municipal Properties
- Minimal Disruption – One morning of leveling can get a shopping‑center sidewalk, a school bus‑lane, or a runway taxiway back in service before evening rush.
- Environmental Stewardship – Modern foams are formulated with ≥39 % recycled or bio‑based content and classified as an environmentally friendly alternative to cement slurry.
- Precision Control – Technicians monitor laser levels in real time, adjusting injection pressure to within 1/10 in. accuracy—critical for ADA compliance and machine calibrations.
- Long‑Term Soil Stabilization – Foam permeates seams, bonds loose aggregate, and reduces water percolation, thereby stabilizing the sub‑grade beneath the concrete surface.
- Less Invasive – Smaller ports keep architectural entryways and polished warehouse floors aesthetically intact.
The Role of Expert Concrete Lifting Teams
Executing a precision slab raising project demands more than equipment. A seasoned crew evaluates soil reports, locates utilities, and uses thermal imaging to identify hidden voids. On leveling day, they regulate foam expansion rates so the slab doesn’t overshoot grade. Post‑lift, they document elevations and provide a warranty—often 5 to 10 years—for professional concrete leveling peace of mind.
Preventive Measures to Ensure Your Concrete Stays Level
While polyurethane solves current settlement, proactive owners mitigate future movement:
- Ensure site drainage directs stormwater away from pavement edges.
- Maintain expansion joints and seal cracks to block sub‑grade washout.
- Schedule bi‑annual surface inspections; early detection keeps repairs small and avoids costly repairs.
When minor dips appear (<¼ in.), early concrete repair using a self‑leveling overlay may suffice. Beyond that threshold, raising and leveling with foam preserves the slab and avoids full replacement—saving 50–70 % compared to pouring new concrete back.
Selecting a Texas Foundation Repair Company
Look for firms that:
- Specialize in polyurethane foam injection for commercial‑scale projects.
- Employ in‑house geotechnical engineers familiar with regional soil chemistry.
- Provide load‑testing data verifying foam compressive strengths >100 psi.
- Carry pollution‑liability insurance for resin handling.
- Offer clear scope‑of‑work proposals, including post‑lift laser‑level reports.
A credible partner won’t just “pump and run.” They’ll explain how different leveling services align with your asset plan, so you can choose the best option for every facility.
Conclusion: Lift, Level, and Lead with Confidence
From Austin’s tech campuses to Port Arthur’s petrochemical corridors, Texas property managers prioritize uptime and safety. With its rapid cure, lightweight chemistry, and proven durability, polyurethane foam injection has eclipsed mudjacking as the best concrete leveling method for slabs that become uneven in the state’s challenging climate. Whether you’re stabilizing a municipal sidewalk, a warehouse driveway, or an airport service road, foam leveling restores concrete surfaces to their original grade—delivering a smoother, safer environment for employees, visitors, and equipment alike.
Ready to lift and level your critical pavement? Contact our team today at Superior Grouting to schedule an estimate and secure long‑lasting stability for your infrastructure.