How Much Does It Cost to Level Concrete in Houston, TX?
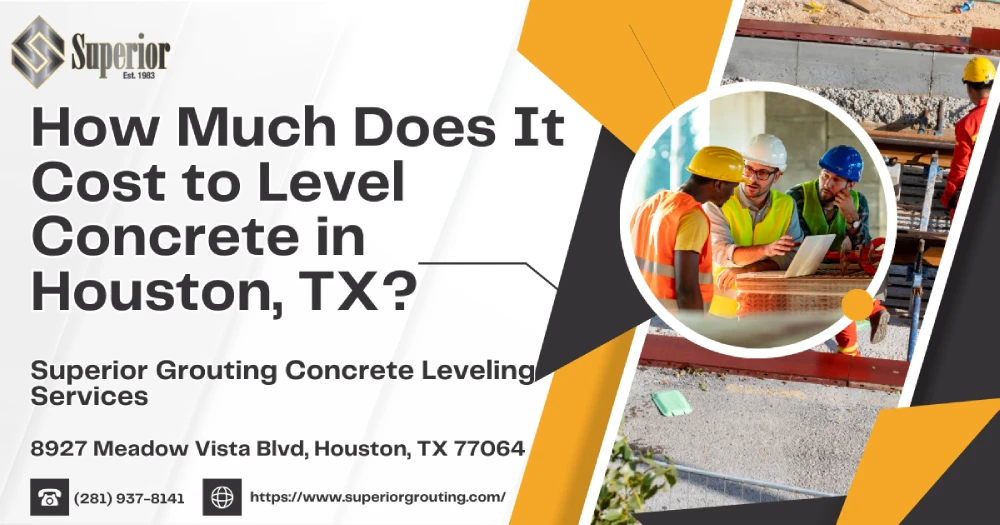
When a critical concrete slab sinks at your Houston facility, you need solid numbers fast. In the Houston area, the concrete leveling cost generally spans $4–$11 per square foot, or $900–$5,670 per job, depending on slab size, accessibility, and whether you choose stone‑slurry mudjacking or polyurethane foam injection.
This guide breaks down every cost driver—material costs, skilled labor, fixed costs, and site variables—so you can secure a fair price, avoid scope creep, and keep your operations moving.
Key Takeaways
- Stone‑slurry grout leveling is the lowest‑priced professional concrete leveling service in TX, averaging $4–$8 per square foot, while delivering high compressive strength for heavy equipment pads.
- Polyurethane foam concrete lifting adds 25–35 % to the overall concrete cost but returns your garage floor, loading dock, or industrial driveway to service within 30 minutes.
- Slab thickness, cubic yards of material, and job‑site access create the biggest swings in cost estimate numbers.
- Houston’s expansive clay soils often demand additional void filling or densification at $1–$2 per sq ft to prevent repeat settlement.
- Request a line‑item quote and a written 5‑year warranty from each concrete contractor to verify you’re paying a fair price—not a guess.
Understanding Commercial Concrete Leveling Services in Houston
Most concrete leveling companies in the Houston market rely on one of two well‑established technologies. Both raise and level concrete with precision, yet each has unique performance traits, material costs, and downtime considerations.
Stone‑Slurry Mudjacking (Pressure Grouting)
- A pump forces a cement‑based slurry blended with locally quarried limestone under the slab.
- As the mix flows, it exerts hydraulic pressure that lifts the slab, fills cracks and gaps, and densifies loose sub‑grade soils.
- Standard concrete cure time is 12–24 hours before forklifts or tractor‑trailers can roll back across the slab.
- Because the slurry weighs more than foam, it counteracts upward soil heave and supports rebar‑reinforced pads carrying extreme loads.
Polyurethane Foam Injection
- A two‑part resin is injected through 5/8‑inch ports; it expands, hardens, and levels concrete in minutes.
- At only 2–4 lb per cubic foot, the lightweight foam minimizes additional downward stress on weak soils, making it ideal for larger projects where soil movement is ongoing.
- Crews can reopen traffic lanes the same shift—crucial for a 24/7 distribution center or high‑volume garage floor.
- Closed‑cell structure repels water, limiting future washout beneath the concrete slab.
Both methods are proven in the concrete industry, but choosing the right approach depends on load demands, operational downtime, environmental goals, and of course, the concrete leveling cost you can justify.
Core Cost Factors That Shape Your Houston Concrete Leveling Project
1. Size and Thickness of the Slab
A 150‑sq‑ft compressor pad may cost only $900 to level, while a 1,200‑sq‑ft distribution‑bay slab can push invoices past $5,000. Thicker concrete (8–10 in.) also requires more slurry or foam, increasing material costs by up to 20 %.
2. Site Accessibility and Job‑Site Logistics
- Easy truck access keeps hose runs short and reduces skilled labor hours.
- Tight interior spaces, elevated mezzanines, or a fenced petrochemical plant may cost an extra 10–15 % because crews must string longer lines or bring in cranes.
- Pour‑and‑finish repairs, joint cutting, or rebar doweling add scope—and dollars—to any leveling job.
3. Soil Conditions Beneath the Slab
Tree roots, washouts, and Houston’s notorious swelling clays all create voids that must be filled and stabilized. If a structural engineer specifies chemical injection or bell bottom piers, plan on $1–$2 per sq ft in additional foundation work.
4. Required Downtime
A facility that cannot pause production often opts for foam. Although the price per sq ft is higher, the cost of replacement downtime far exceeds the premium for rapid return‑to‑service.
5. Permitting, Traffic Control, and Compliance
Depending on the area, a City of Houston permit may cost $85–$300. Traffic‑control setups, safety barriers, and on‑site inspectors from a third‑party foundation company can add a fixed cost of several hundred dollars.
Typical Price Ranges in Houston, TX
Method | Typical Slab Category | Average Sq Ft | Ballpark Cost Range | Return‑to‑Service |
Stone‑Slurry Grout | Equipment Pad | 150–300 | $900–$1,800 | 12–24 hrs |
Stone‑Slurry Grout | Loading Dock / Driveway | 400–800 | $1,800–$4,200 | 12–24 hrs |
Polyurethane Foam | Equipment Pad | 150–300 | $1,215–$2,400 | 30 min |
Polyurethane Foam | Dock / Garage Floor | 400–800 | $2,400–$5,670 | 30 min |
These numbers assume standard concrete, minimal rebar interference, and unobstructed pump access. They give you a ballpark before requesting a detailed cost estimate.
Comparing Long‑Term Value: Slurry vs. Foam
Performance Factor | Stone‑Slurry Grout | Polyurethane Foam |
Weight | Heavier; stabilizes under high wheel loads | Ultra‑light; ideal for weak soils |
Cure Time | 12–24 hrs | 15–30 min |
Environmental Impact | Locally sourced limestone | Petrochemical resin |
Cost Per Sq Ft | $4–$8 | $6–$11 |
Warranty Typical | 5 year warranty | 5 year warranty |
Slurry’s added mass excels under container lifts or heavy mobile cranes. Foam’s speed can save thousands in downtime for logistics hubs that never shut down.
Hidden Costs Most Facilities Miss
- Joint & Crack Sealing: Level concrete still needs polyurea or epoxy joint filler at $3–$7 per linear foot to prevent water infiltration.
- Surface Grinding & Coatings: A fresh, flush finish may cost another $0.50–$1 per sq ft, especially on polished warehouse aisles.
- Soil Densification: Chemical grout injections under slabs with chronic moisture issues may cost 10–15 % of the total leveling project but can eliminate repeat settlement.
- Engineering & Testing: A structural engineer’s DCP test or ground‑penetrating radar scan usually runs $400–$700 but verifies bearing capacity and rebar location.
How to Secure a Fair Concrete Leveling Cost in Houston
- Schedule an on‑site walk‑through with at least two professional concrete leveling services.
- Ask each contractor for a line‑item proposal: material volume, price per cubic yard, labor rate, cleanup, and warranty terms.
- Require proof of insurance, references from similar industrial slabs, and clarity on who pays if unexpected voids inflate material costs.
- Demand a written 5‑year warranty covering lift loss greater than 1/4 inch.
- Get a free estimate in writing—never rely on a phone ballpark for a complex job site.
The Bottom Line
In the Houston market, professional concrete repair through pressure grouting or foam injection typically costs $900 to $5,670, or $4–$11 per square foot. Slurry offers a lower entry point and heavyweight support, while foam delivers rapid reopen times and water resistance. Because material costs, slab thickness, and soil conditions vary from one job site to the next, always request multiple quotes, compare warranties, and consult a structural engineer when foundation repair may be needed. By following the steps above, you’ll lock in a competitive price, restore structural integrity, and keep Houston operations running smoothly.
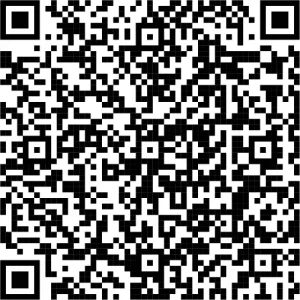